Clean Concrete: Making the Building Blocks of Society Sustainable
11 minute read
Updated on: 29 Aug 2021
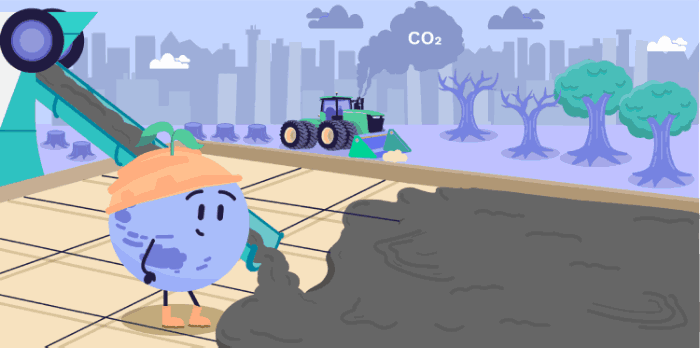
What is concrete and why do we need it?
Concrete is a strong, long-lasting, and versatile building material that has been extremely important in the creation and expansion of cities across the globe . The worldwide demand for this material is huge:
Concrete is second only to water as the most used material on the planet ! Unfortunately, because of its process of manufacture, this means that concrete production is responsible for a whopping 8% of global CO₂ emissions
.
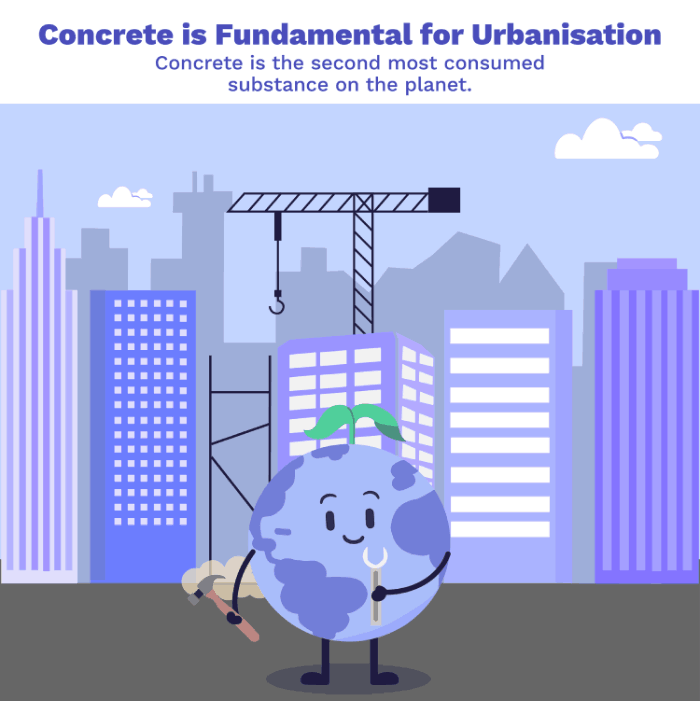
Concrete is the second most consumed substance on the planet
How is concrete made?
Concrete contains three main components: aggregates (a mixture of sand, crushed stone, and gravel); a paste made from water and cement (which acts as the glue); and air !
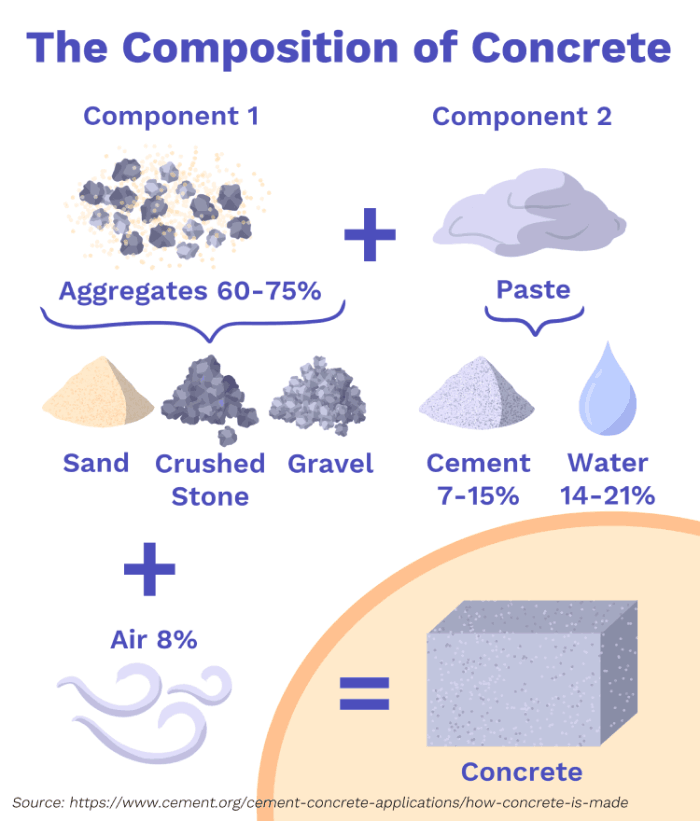
What is concrete made of?
Cement is a key element in concrete and is made out of gypsum, a soft mineral, and clinker, a lumpy solid that is made by burning calcium carbonate and other oxides in a kiln
.
The manufacturing of clinker is based on a chemical reaction called limestone calcination . In this process, calcium carbonate (CaCO₃) - commonly known as limestone - is broken into calcium oxide (CaO) and carbon dioxide
.
What are the environmental impacts of concrete and cement?
All of these are impacts of the concrete and cement industry and exist on a local, regional and global scale.
- Local impacts: During the limestone calcination process, cement kiln dust (CKD) is released
. When not collected properly, CKD can pollute water, soil and air
. It can also cause skin burns, eye damage, and even respiratory irritation or cancer because it is small enough to be inhaled
.
- Regional impacts: During cement manufacture, the burning of fuel emits sulfur dioxide (SO₂) and nitrogen oxides (NOx)
, both major contributors to acid rain
.
- Global impacts: On a global average, the production of 1 kg of cement generates approximately 0.81 kg of CO₂
.
Surprisingly, most of its impact comes from cement manufacturing, which accounts for 90% of emissions from concrete .
Around 30% to 40% of direct CO₂ emissions come from fuel combustion for heat and electricity production, 50% to 70% are released from limestone during the limestone calcination (cement manufacture) process outlined above . The remaining emissions (up to 10%) are considered indirect emissions and are usually caused by transportation
.
The worldwide demand for cement is expected to grow by 30% by 2040 . If we don’t do something about the CO₂ emissions from current concrete production, growth in this industry will be a major contributor to climate change
.
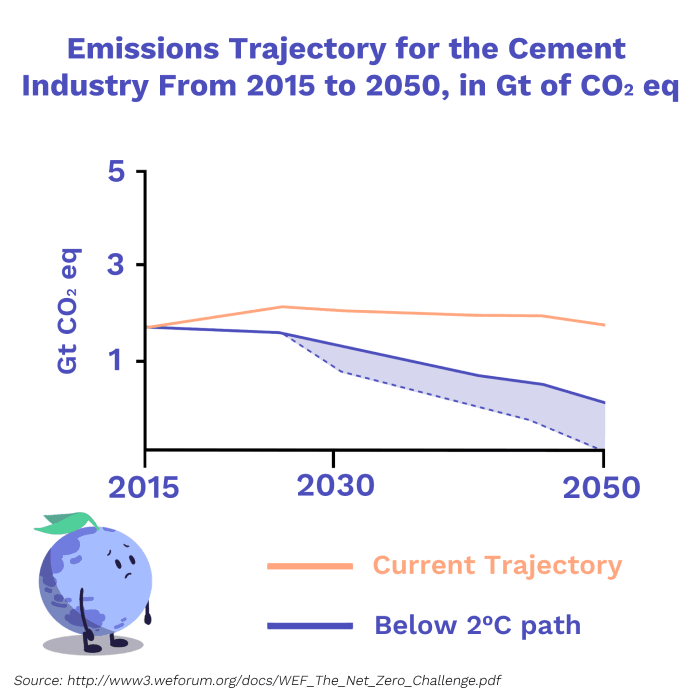
We need to cut cement emissions, fast!
Can we make concrete without emitting CO₂?
In accordance with the Paris Agreement, to limit global temperature increases to 2°C, direct CO₂ emissions from cement and concrete production need to be cut by 25% by 2050 .
The most promising solutions include :
- Improving energy efficiency
- Using alternative fuels
- Using different clinker materials
- Implementing carbon capture, utilisation and storage (CCUS)
- Using carbon-negative cements
1. Improving energy efficiency: Improvements in energy efficiency during cement manufacture could reduce direct CO₂ emissions by up to 12% . About 65% of the thermal energy demand comes from the kiln, where heat energy is absorbed by the reactions needed to transform limestone into clinker, while the remaining ~35% is used to dry the limestone
.
How can we reduce the energy demand? There are a couple of options:
Dry process kilns: Limestone is exposed to a long-dry preheater to reduce its moisture content , so less heat is needed to evaporate the water and the limestone can undergo calcination faster
.
Excess Heat Recovery (EHR): During the whole cement manufacturing process there is a lot of waste heat that can be easily collected and reused
.
Reducing electrical demand in cement grinding: Throughout cement manufacturing, the greatest electrical demand comes from cement grinding (31% to 44%) . For the last 100 years, plants have been using ball mills for grinding cement and raw materials, which consume about ~30 kWh per tonne of material fed
. This amount of energy could power the average british home for almost three days
!
Fortunately, there exist alternatives that consume less energy. High pressure grinding rolls (HPGR) crack the cement when exposed to high pressures between two rolls, creating smaller particles . In comparison to ball mills, HPGR can represent an energy saving of 30% - 50%
. Vertical roller mills (VRM) use an airstream to force small particles to leave the mill while the rest remain for further grinding
. VRM are capable of producing finer particles than ball mills and also use 70% less energy
.
However, these technologies face some implementation challenges, such as high investment cost .
2. Switching to alternative fuels: In cement production, fuel is used to produce heat in the kiln and calciner. On a global average, 70% of this fuel comes from coal, followed by 24% from oil and natural gas and less than 6% from alternative fuels .
We need physical fuels that can be fed into and burned inside of the kiln and calciner, so nuclear and wind won’t work, but biomass and waste products can! Instead of carbon-intensive fuels, biomass and waste materials can be fed to the kiln and calciner . In principle, they could substitute 100% of the fuels used in the kiln and up to 60% in the calciners
. Using these alternatives to fossil fuels could prevent up to 42% of current direct emissions in the cement industry
!
3. Reducing clinker-to-cement ratio: Producing 1 tonne of clinker releases around 0.706 tonnes of CO₂ . Nevertheless, clinker can be substituted with alternative materials with low carbon footprints or even zero net emissions
, such as granulated blast furnace slag (GBFS), fly ash (FA), pozzolanas and limestone
.
The use of these alternatives depends on many factors, mainly availability and price. Also, it is important to consider how the properties of the cement will be changed by using these alternatives .
4. Carbon capture utilisation and storage (CCUS): CCUS consists of capturing CO₂ as it is emitted and then compressing it into a liquid in order to store it deep underground (CCS) or to use it to make new products (CCU)
. Although CCUS technology is still in industrial trial phases, it shows promising results for use in the cement supply chain
. The different types of CCUS technology will be covered in detail later in this course!
5. Carbon-negative cements:
Carbon-negative cements have the potential to store more CO₂ than they actually emit during their manufacturing process! One way to do this is by using magnesium-oxide based cements, which could potentially absorb and store CO₂ from the environment . How does this work?
As its name states, the main raw material in these cements is magnesium oxide (MgO), which is burned in order to produce a clinker called caustic calcined magnesia (CCM) . When CCM is hydrated it becomes brucite (Mg(OH)₂), a component that is transformed into magnesium carbonate (MgCO₃) when exposed to the atmosphere; this basically means it absorbs CO₂ from the air
.
Although this technology is still being developed, it shows promising results for the future, as it could potentially absorb more CO₂ than is released throughout the production chain ! Currently, there are many companies producing interesting carbon-negative cements, such as CarbonCure
and Novacem
.
Conclusion
Concrete is a widely used and important material whose production is a big contributor of worldwide CO₂ emissions. Fortunately, as we’ve seen, there are many promising decarbonisation pathways and interesting developments taking place (either by modifying the manufacturing process, using alternative sources of energy and prime materials, or by changing the composition of concrete itself), and more will keep emerging in the future! With this insight, the future is clear: the concrete and cement industry can and must be transformed to meet global climate goals .