Oxy-Fuel: Burning Carbon in Pure Oxygen to Help the Climate
9 minute read
Updated on: 15 Jul 2021
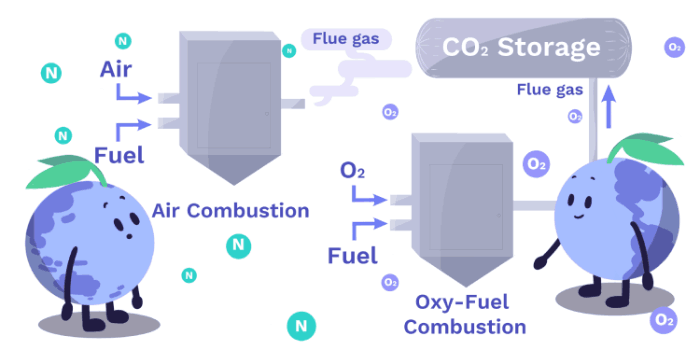
Oxy-fuel combustion is a new and inventive way to deal with emissions from burning fossil fuels in power plants.
What’s the difference?
Traditional power plants release flue gas (smoke from combustion released via smokestacks) directly into the atmosphere. All the pollutants it contains, such as CO₂ and NOₓ, are released with it . Oxy-fuel power plants, on the other hand, capture the flue gas (which is rich in CO₂) to compress it and then store it
.
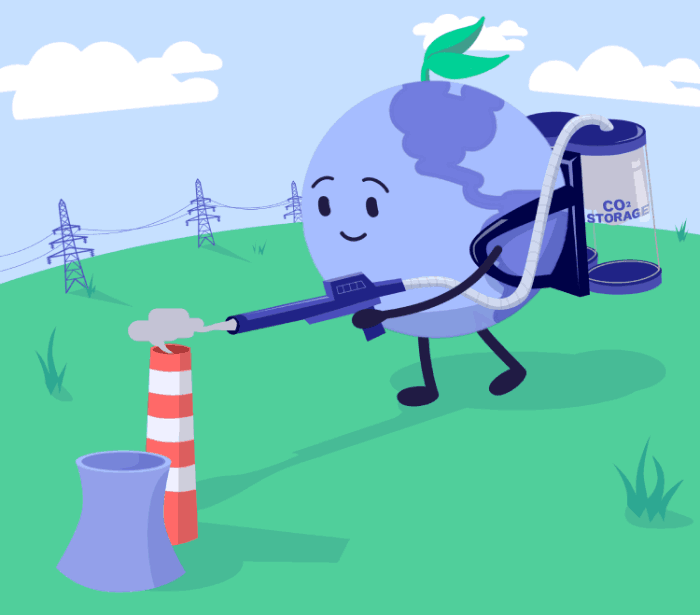
Removing and storing CO ₂
Flue gas from an oxy-fuel plant has CO₂ in very high concentrations compared to a normal power plant. Why is this a good thing? Well, let’s first learn what oxy-fuel combustion really is.
What is oxy-fuel combustion?
In oxy-fuel combustion methods, fossil fuels are burnt in almost pure oxygen instead of regular air .
We can see that nitrogen makes up the majority of air . By removing nitrogen from the air in which the fossil fuels are burnt we can produce flue gas with very high concentrations of CO₂ and H₂O
. This concentrated flue gas is much easier to compress and store.
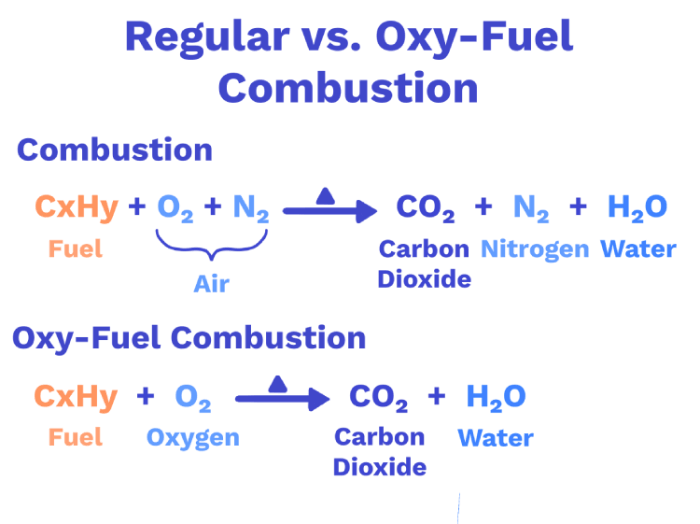
Oxy-fuel has higher concentrations of CO₂
How does oxy-fuel combustion work?
The diagram above was a very simplified model of the combustion process. Below we can see what’s going on in more detail:
First, oxygen is separated from nitrogen in an air separation unit via cryogenic air separation (a separation method in which air is cooled down to the point where various gases turn to liquid
). Because the temperature of liquid oxygen is -183℃ and liquid nitrogen is -195.8℃, we can make oxygen liquid and separate it from nitrogen gas
.
Next, the fuel is burnt with nearly pure oxygen in the boiler. This produces electricity as well as flue gas containing CO₂, H₂O and some impurities .
The water in the flue gas is cooled to a liquid, leaving even more pure CO₂ in the mix .
Do you see a pipe labelled “recycled flue gas”? This pipe takes a large part of the flue gas to mix together with the oxygen and fuel in the boiler.
In fact, around two-thirds of the flue gas is recirculated (recycled) back into the boiler to control its temperature .
How does it control the temperature?
When coal burns in pure oxygen the flame temperature can reach 2800℃, compared to 2000℃ with air . There are no boiler and burner construction materials today that can withstand such a high temperature
.
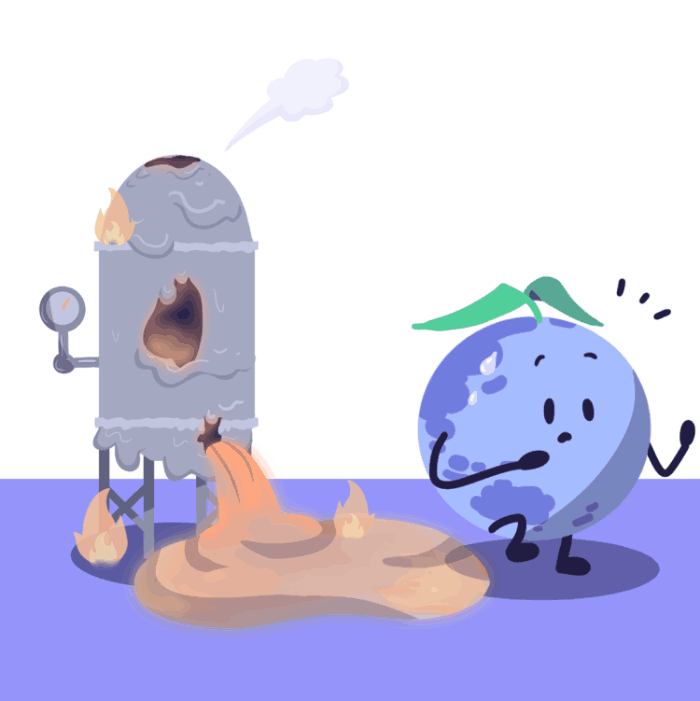
No boiler or burner materials can withstand 2800℃
Therefore, adding some CO₂-rich flue gas helps lower the temperature to a level similar to that in a traditional air-blown plant .
This is also what provides such a high concentration of CO₂ in the flue gas stream, at around 60-70% . This is in contrast to the 12-14% concentration of CO₂ in flue gas when normal air is used
.
A high concentration of CO₂ avoids the problem we saw in previous chapters, where nitrogen in the flue gas mixture made it harder to separate CO₂ .
Another major advantage is that the size of the combustor may be reduced to one fifth of that used in air fire combustion .
If we compare this process to the post-combustion CO₂ capture we learnt about in the last chapter, it uses less energy and produces fewer greenhouse gases .
What are some of the challenges this technology faces?
The oxygen separation at the beginning of the process is usually carried out cryogenically (where gas turns into liquid). To reach such low temperatures, this method requires around 220kWh of energy per tonne of oxygen generated . For a typical 500MW coal-fired power plant, supplying the pure oxygen would require around 15% of all its electrical output
. In fact, the large power requirements for both the oxygen production and the CO₂ compressor would reduce the energy efficiency of the power plant by 25-30%
. This means that this is currently not a cost effective method of energy production for most power plants
.
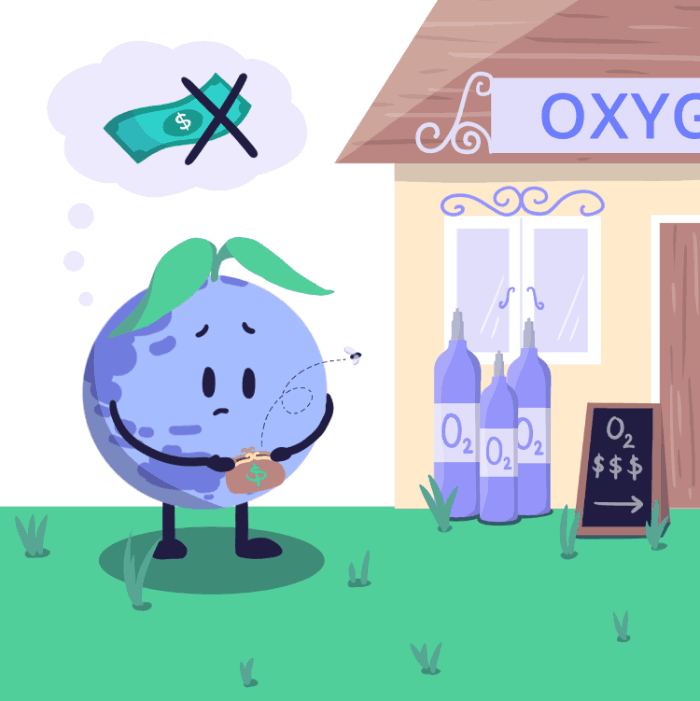
Earthly doesn’t have enough money to buy oxygen
Exactly how much would it cost?
Since the oxy-fuel process is expensive and uses a lot of energy, the cost of electricity generated in oxy-fuel plants increases drastically from US$66.8 per MWh in a normal power plant to US$123.7 per MWh .
This is quite expensive for just one tonne of CO₂!
The price of electricity produced using oxy-fuel is similar to using post-combustion capture in coal plants. In terms of costs, that means there’s not much to choose between this and some of the methods from the previous chapter .
Where would we use oxy-fuels?
Coal and gas plants are best suited for this technology . It’s currently being tried out in a couple of places around the world, including Schwarze Pump in Germany and the Callide 30 MWe Demonstration Plant in Australia.
What will it be like in the future?
The overall oxy-fuel process is currently only being demonstrated, and we don’t yet know if it will be effective on a global scale .
The biggest challenge is the cost of getting oxygen, though there are some possible solutions.
One option is called oxygen chemical looping combustion . This method involves two reactors and removes the need for an air separation unit
.
In the first reactor, a solid ‘oxygen-carrier’ is heated in air and captures oxygen. It, therefore, becomes a solid oxide .
These oxygen carriers are typically from a special group of metals known as transition metals:

Types of oxygen carriers
In the second reactor, coal is gasified to produce syngas (remember - gasification is when you react coal with oxygen to give syngas, a mixture of mostly CO and H₂) . The ‘oxygen-carrier’ is then moved to the second reactor. When mixed together, the oxygen from the carrier reacts with part of the syngas to produce electricity
!
The challenge is to find a good oxygen carrier that is cheap, holds enough oxygen and can be reused many times .
We’ve been learning a lot about different CCS technologies. Let’s look at a table comparing their cost , plant efficiency
and the stage of progress for each technology
.
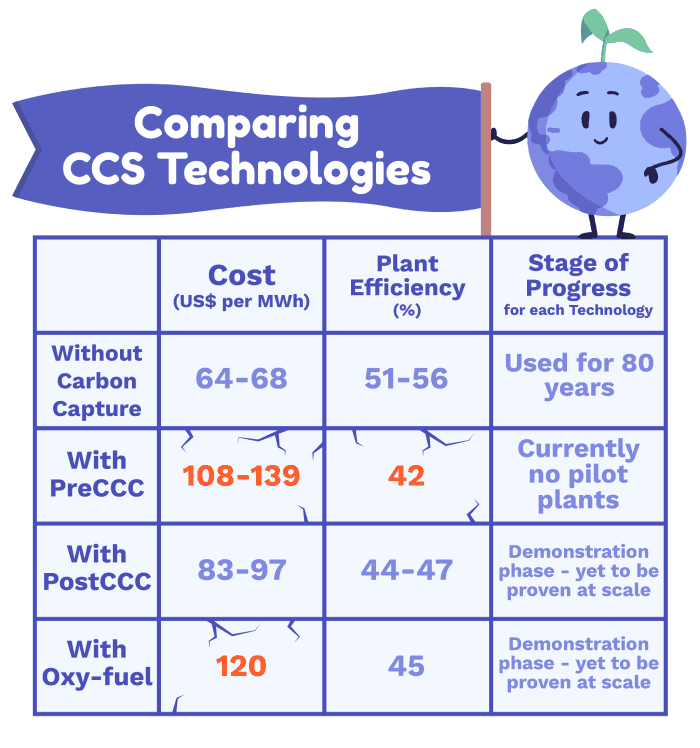
Costs and efficiencies of using different CCS technologies
We can see that the cost per MWh of electricity for traditional power plants are much lower than for those with CCS technologies. We also notice that plant efficiency is lower for CCS technologies. As they are all still being researched, hopefully the costs can be lowered and efficiency raised to cut future CO₂ emissions.
The last three chapters have explained how we can capture CO₂ to prevent it from entering our atmosphere. What exactly can we do with this carbon once it’s captured? Read the next chapter to find out!
Next Chapter